Precision Cleaning
Advanced Deburring & Finishing is proud to offer a family of precision cleaning systems to answer the industry’s needs for solvent-level cleaning solutions without environmental complications. This solution utilizes non-chlorinated hydrocarbons in a closed-loop system to provide superior results with virtually no emissions.
This leading-edge technology was developed in Germany to satisfy stringent European regulations making the use of chlorinated solvents impractical. The technology, first introduced in Europe in 1995, has gained considerable recognition after numerous successful installations. Systems have been sold and installed in the United States, primarily replacing cleaning systems that failed to meet the process requirements after customers were forced to transition away from conventional solvent solutions due to costs and risks related to environmental issues.
The system incorporates a number of unique features. Some of these features are common across this entire family of cleaning products, which include aqueous cleaning systems as well. All of the systems in this family of products are built as self-contained, compact units, minimizing installation costs.
Contact Us for Your Precision Cleaning Systems
All machines utilize a high degree of stainless steel, not only in tanks and chambers but also in components such as valves and pumps. All units incorporate a single cleaning chamber that facilitates complete submersion of the component(s). High-pressure pumps offer Injection Flood Wash circulation options. Vacuum drying and ultrasonic cleaning are available in all units in this family.
User-defined part rotation from 10 degrees to 360 degrees is also standard in all units with part-specific process recipes stored and retrieved via a friendly Man-Machine Interface.
Complete process flexibility is configurable via these recipes. Both aqueous and solvent-based systems are available with closed-loop solution circulation systems for emissions-free operation.
The non-chlorinated hydrocarbon units utilize a distillation system that continuously circulates the solvent. The solvent is evaporated and reclaimed to provide complete separation of contaminants. Contaminants are accumulated in an easy-to-clean container for proper disposal. Vapor degreasing can also be done in this single-chamber system.
A typical cleaning cycle follows this pattern:
1. Load part and close chamber door
2. Evacuate air from the chamber
3. Submerge, rotate 120 degrees with oscillation and Injection Flood Wash circulation
4. Empty chamber and draw vacuum
5. Vapor degrease
6. Vacuum dry
7. Backfill chamber with plant air
8. Open door.
Other significant benefits of this non-chlorinated hydrocarbon system are its inherent flexibility to process a wide range of materials without complicated chemistry modifications. Additionally, for materials such as brass that leave lead byproducts in aqueous-based cleaning systems necessitating the regulated disposal of the wastewater, this system can offer considerable savings.
When compared to conventional aqueous precision cleaning systems, this system typically utilizes 60% less energy, requires less maintenance, handles higher oil loading levels and provides superior cleanliness and spot-free results continuously.
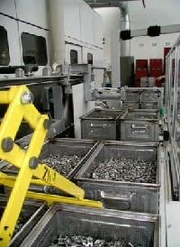
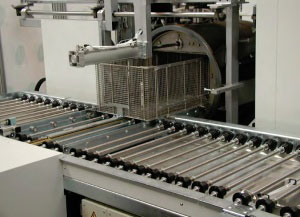
Precision cleaning systems are all about conducting a cleaning process in an efficient and sustainable manner, from coarse to intermediate to ultrafine cleaning. After the continuous distillation of the cleaning medium, a fresh cleaned solution is used in the final step for the best results.
Our compact systems meet cleaning requirements with a small footprint. The overall dimensions are:
Overall Dimension:
- Width: 1000 mm
- Depth: 2100 mm
- Height: 2600mm
Features:
- Basket size: 320-380mm L X 220mmW X 150-200mm (max)
- Weight Capacity: 50kg
- Working envelope based on working chamber size
Polar CleanING vs. Non-Polar CleanING
Have you heard of polar cleaning and non-polar cleaning? What is polar vs. non-polar?
- Non-polar are oils and solvents
- Polar are salts and water-based
The greater the electronegativity difference, the more ionic the bond is. Bonds that are partly ionic are called “polar covalent bonds”. Non-polar covalent bonds arise when the electronegativity of the two atoms are equal.
Non-Polar Molecule:
A non-polar molecule is a molecule in which the electrons are shared equally between the nuclei. As a result, the distribution of charge is even and the force of attraction between the different molecules is small.
The EcoCore is a fully enclosed system with many available features:
- Higher load capacities
- HMI panel integrated part visualization
- Adaptable operation
- High flexibility with the cleaning process
- exceptional ease of maintenance and solution care
Basket Size:
- 1 at 670mm X 480mm X 400mm
- 4 at 480mm X 320mm X 200mm
Capacity: 200kg
There are many different basket configurations available for multi-part washing/separation to maximize loads.
|
|
|
New technology is demanding and needs precision cleaning for the reliability of a finished product part or consumer product. Sophisticated system designs such as the EcoC Wave, Mega 86W and the 81W universal are engineered for precision and offer versatile options for your applications, production needs and assurances.
Units are self-contained and compact, minimizing installation costs. All machines utilize a high degree of stainless steel, not only in the tanks and chambers but also in components such as valves and pumps. All units incorporate a single cleaning chamber that facilitates complete submersion of the component(s). High-pressure pumps offer Injection Flood Wash circulation options. Vacuum drying and ultrasonic cleaning are available in all the units. User-defined part rotation from 10 degrees to 360 degrees is also standard in all units with part-specific process recipes stored and retrieved via a friendly machine interface.
- Sample part processing is so important and valuable when looking at surface cleaning.
|
|
A distillation system continuously circulates the solvent. The solvent is evaporated and reclaimed to provide complete separation of contaminants. Contaminants are accumulated in an easy-to-clean container for proper disposal. Vapor degreasing can also be done in this single-chamber system.
EXAMPLE - Precision Cleaning |
||
---|---|---|
BEFORE | ||
![]() | ![]() | ![]() |
AFTER | ||
![]() | ![]() | ![]() |
Precision Cleaning with Immersion, Agitations or SoniCs
Delicate Cleaning for High Cleanliness Requirement
This Precision Wash Rinse Dry System was built for cleaning components prior to FPI. It processes a complete family of large cylindrical parts used for aerospace. The system achieves very high cleanliness specifications in accordance with the manufacturer’s requirements. The line is constructed from four stainless steel modular CM Systems and runs left to right. The entire line is built upon a heavy duty I beam fabricated base for accuracy, stability, ease of shipping and installation. A safety light curtain traverses the front of the system.
The photo above shows the front of the system. The control pedestal (center) includes a main Nema 12 panel with the air over oil tanks and flow controls mounted behind the control box. Note that nothing is placed underneath the processing tanks or tucked behind the “access” panels. All valves, pumps, filters, cylinders and heaters are located outside of the console where they are accessible, clearly visible for inspection and easily serviced. RAMCO automated systems are designed for industrial applications.
Components are loaded into baskets and placed on a load lifting conveyor (above, far left). The lift section automatically raises the basket to the correct processing height for lateral transfer through the precision cleaning system.