Last updated on October 12th, 2021 at 06:30 pm
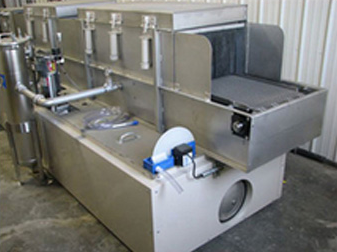
Multi-Stage In-Line Conveyor Parts Washers
Flat Belt pressure Spray Washer
Put Super Spray continuous flow washing systems to work washing your parts. Part parameters and flexibility in the design is key for flat belt cleaning. Parts travel through the tunnel on a flat or woven wire belt with contaminants being removed by powerful water spray in combination with a specified cleaning agent, temperature and/or adjustable/different spray nozzles.
Part process through the system is based on production numbers needed and surface feet per minute on the belt speed. Sample part processing can evaluate and validate sizing, pump pressures and processing stages needed to meet the finished part specification.
Standard system configuration uses heated wash zones, rinse zones, and blow-off or hot air dry finish depending on the part parameters. Filtration and oil separation are always very important for part and solution quality in continuous flow washing systems.
Contact Us for Your Continuous Flow Washing System
3-Stage Wash, Rinse/Inhibit and Blow-off Dryer Conveyor Washing System
Variable speed stainless steel belt, all stainless steel construction, 2 filtration units, moisture blow-off section with 10Hp regenerative blower, 6 each 15kw heaters (4 for wash, 2 for rinse), automatic solution make-up system, removable stainless steel chip basket, exhaust duct connections and emergency stop button on both ends.
Benefits:
- Minimum shop floor space required for increased productivity per square foot.
- Reduced materials handling with production number increase means labor savings.
- Quick access to features and tanks for minimal maintenance procedures means less downtime.
- A multitude of applications for general surface part cleaning according to stringent cleanliness specifications for aerospace, automotive, stamping operations and bearing blanks/races.
Concept With flow-through or continuous flow cleaning systems:
The basic idea behind conveyorized continuous flow cleaning systems is based on the concept of high throughput continuous flow with minimal handling of parts during the cleaning, precoating, surface preparation and preassembly stages.
Systems can come with two different drive systems: Fixed-speed for single/dedicated products or variable-speed for a wider range of different products to be processed through the system.
Pumping sizing can be of extreme importance in any washing system. Several factors must be considered for pump sizing with volumes and pressures:
- Area to be covered (part parameters)
- Materials to be removed from product
- Speed and production rate
Multi-stage systems can incorporate closed-loop solution systems for recirculation of cleaning medium and rinse-to-drain for rinsing with Rust Preventative or DI Water prior to a drying/blow-off stage.
360 spray nozzle/manifold setup
Quick Disconnect
Many nozzle styles are available for different directions and cross-flow spray patterns.
Standard Size Systems:
Belt Width | Tunnel Height | Wash/Rinse Zone | |
PW 12-48 | 12″ | 12″ | 48″ hood 3′ spray with manifolds |
PW 18-48 | 18″ | 12″ | 48″ hood 3′ spray with manifolds |
PW 24-48 | 24″ | 24″ | 48″ hood 3′ spray with manifolds |
Semi-automated systems with minimal operator intervention to load/unload parts. Single plant location. Indexing belts start and stop at each stage, where robotic implements/automation can work to load or unload production.
Baskets and fixtures all can be utilized with these methods of cleaning.
Model: PWB24-48E
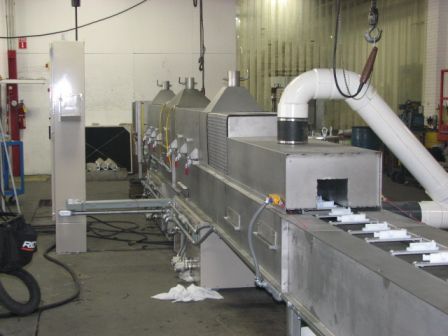
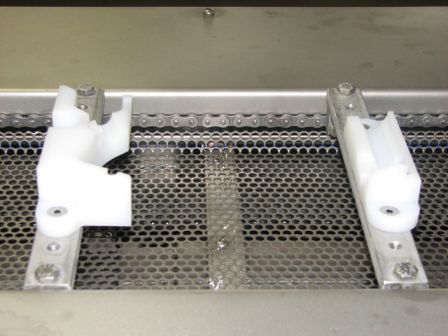
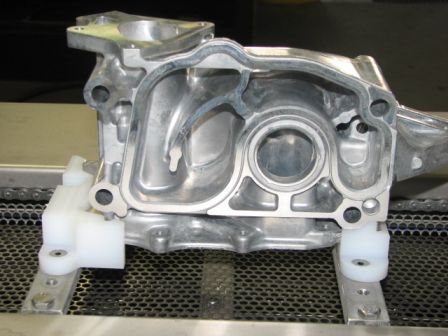
DRYing
How dry is dry?
Absolutely dry usually calls for a true heated dryer running at 235 as a part passes through.
Blow-off dry is another preferred method throughout our industry. Its function is to remove water droplets to greatly assist flash drying using stored part temperatures to evaporate moisture on the surface.
What is the difference between regenerative and centrifugal blower systems?
Regenerative:
Offers a combination of a blower and a low-pressure compressor. These warm the air delivered by anywhere from 30 to 50 degrees above the surrounding air. Typically used to “squeegee” water off of relatively flat and smooth surfaces.
Centrifugal:
These are high-volume/high-velocity blowers where blind holes, recessed or large areas with varying surface profiles need water droplets or moisture removed. Having a means for the air to exit the unit is a primary concern for these blow-off systems.
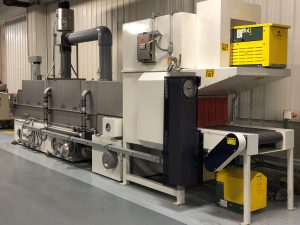
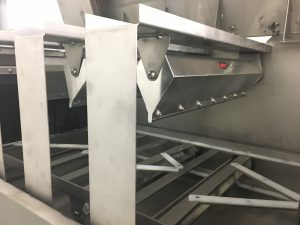
There are so many different configurations that can be custom-designed for your procedure.
“U” Bend belt conveyor style spray washing system
All stainless steel, multi-stage continuous flow, filters, quick set, clip nozzles available and special “U” bend design. Provides a single plant location for the operator (load/unload) and conserves valuable floor space.
Monorail and Trolley Systems
These use fixture tree assembly on a moving overhead trolley chain system. Parts loaded on the tree to go through hang-on stages within the system.
Separate cleaning or combined with paint, powder coat, blasting and turnkey systems for non-stop raw to finished parts.
Rotary Drum
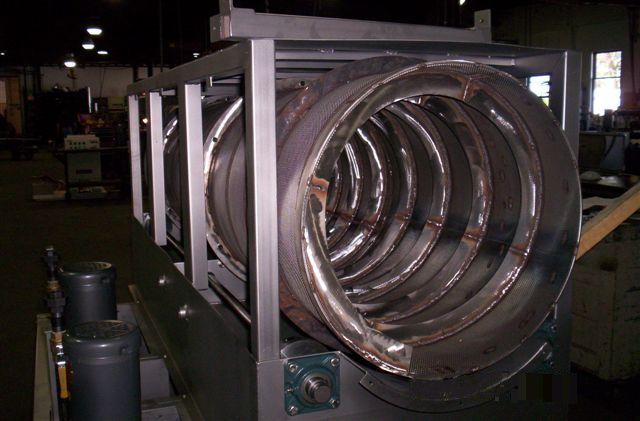
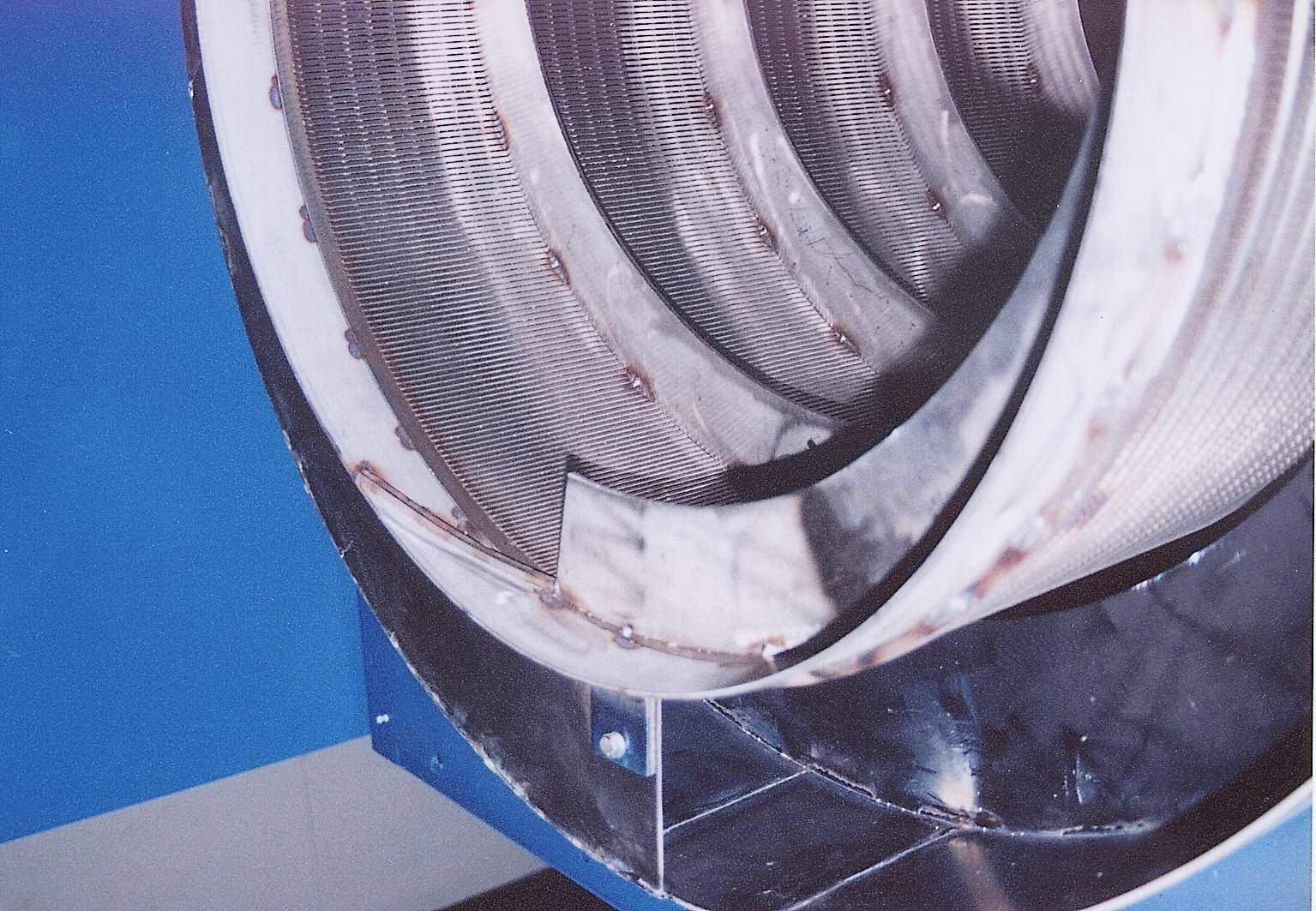
Rotary drum type continuous flow washing systems can do high-volume production with no manual attention needed for continued production, similar to belt-style units. We have a specified auger size the entire length of our drum. The major difference with this process is that the parts tumble, which delivers some benefits so long as contact is okay.
Cleaning zones are similar with wash, rinse and/or blow-off/hot air drying. The first section is a solid drum, as parts are immersed in the cleaning solution as the main spray manifold extends down through the drum, spraying the solution under pressure. Immersion stage to perforated or wire drum for spray cleaning.
As our drum rotates, the fixed auger moves the parts forward through the stages in the rotary drum cleaning system. Single-stage machines and multi-stage machines are available depending on your finished parts specifications.
Standard drum sizes: 12″, 18″, 24″ and 30″ diameter.
Suitable for water-based and rust-inhibiting cleaning capabilities and parts drying.
Contact Advanced Deburring & Finishing for the Continuous Flow Washing Systems you need.
Contact Us Give Us A Call