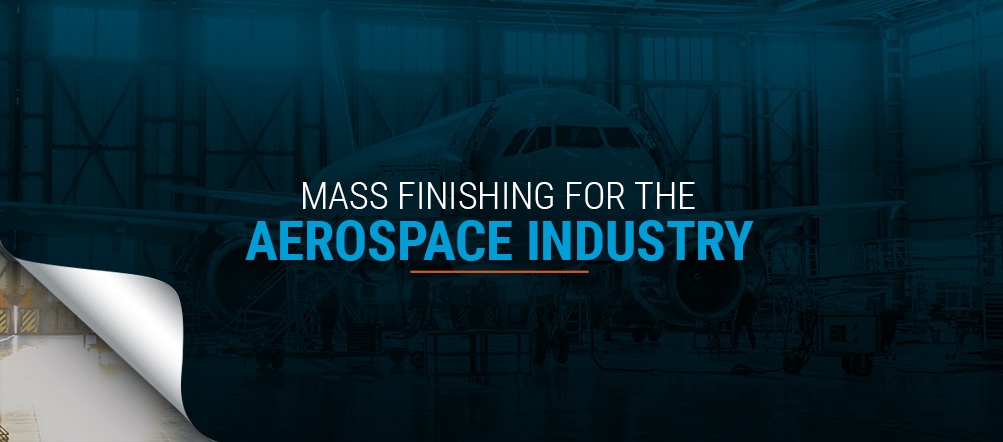
January 13, 2021
Last updated on August 23rd, 2024 at 06:47 pm
The process of making an airplane is extremely complex. It starts with the engineers creating the design, then comes the manufacturing of the different parts and their assembly. Once the aircraft is assembled, it is rigorously tested to make sure all parts work as they should. When testing is completed and all the aesthetic and decorative elements are installed, the aircraft is ready for use. All of these steps are essential to ensure the aircraft flies properly and complies with the necessary safety requirements upon its completion.
But what many people might not realize is that some of the most surface-level elements — the most literal ones, no less — are also some of the most critical steps in the process. Metal finishing for aerospace parts is a step that no manufacturer can afford to skip.
What IS Mass Finishing?
Mass finishing involves the execution of multiple finishing processes — such as deburring, which involves the smoothing of sharp edges — for many metal parts at once. Any manufactured metal parts are likely to go through this process. These parts could accomplish many different tasks, but they frequently appear in machinery or as exterior plating to something, like a vehicle.
The goal of finishing is to ensure metal parts are smooth and polished, removing inconsistencies on their surface. This smoothing can be done by adding a thin layer of metal on top, by grinding down uneven metal from the original or by using some combination of the two. A variety of different finishing systems can accomplish this treatment. When these systems are brought together into one overall process and applied to a large number of metal pieces at once, we can call it mass finishing.
Mass finishing can be highly useful in many different industries, particularly those that involve complex engineering and manufacturing, such as the aerospace industry.
What Types of Finishing Systems Are There?
Finishing can be broken down into a long list of processes, some of which can be divided even further. Of these different system types, however, some stand out more than others based on how widely they’re used. These are eight of the main systems used in mass finishing:
- Metal plating: Coating a surface in a thin layer of metal, often by using electricity to layer metal ions smoothly across the surface
- Brushed metal: Using an abrasive belt or brush to sand down any imperfections on a surface
- Grit Blasting / Sand Blasting: Shooting sand or similar material into a surface at high pressure, thus knocking away loose flakes and flattening the rest
- Vibratory finishing: Putting a part into a drum filled with small pellets and spinning it around so that the pellets wear it smooth
- Buff polishing: Buffing a surface using a cloth wheel to sand away imperfections and give it a glossy sheen
- Powder coating: Coating a surface with a glossy paint-like substance, similar to metal plating
- Hot blackening: Spreading a black oxide layer onto a surface using high temperatures to make it abrasion-resistant
- Metal grinding: Rubbing another metal across a surface to create enough friction to smooth out imperfections
Each of these systems constitutes a broad type of finishing process, but different versions of each one exist. For instance, metal plating can be done through electroplating, or through electroless plating. Electroplating uses an electric current to deposit metal ions on a surface, while electroless plating does so without electricity, solely through chemical processes.
Questions? Contact Our Team Of Experts Today
How Is Finishing Used in Aerospace?
In light of the number of systems at work in mass finishing, how do these processes relate to aerospace? As it happens, aerospace is one of the industries where finishing is most important. Given that airplanes must safely carry people, travel over short and long distances and be able to withstand a variety of atmospheric conditions, it’s incredibly important to ensure the engineering involved in their construction is executed to perfection.
For all aerospace deburring methods, everything comes down to the smallest details, such as in the engines. To keep the plane in the air, the engines have to operate smoothly. This means all the intricate metal parts within those engines must fit together perfectly. If even a single piece gets jammed, it could cause major repercussions. All the parts making up the engines need to be completely smooth, without any surface defects that could keep them from functioning the way they’re supposed to.
Mass finishing is the answer to this need. It’s frequently used for things like engine compressor blades, minimizing friction with the parts they attach to, and, therefore, optimizing their ability to spin. Finishing also applies to much larger areas of the plane, however. The exterior of every airplane is sprayed with a finish that, among other things, allows the paint to adhere better to its surface.
What Are the Benefits of Metal Finishing?
There’s a reason deburring and finishing are so widely used and so important. They provide multiple benefits to the metal parts that are put through the process, making them much better in terms of both performance and appearance. Here are some of the main ways metal finishing improves equipment:
- Limits corrosion: Smoothing away the microscopic gaps and inconsistencies in the metal makes it harder for corrosion to form on the surface.
- Improves durability: If a metal part already has a rough and inconsistent surface, it’s easier for it to acquire further damage. Smoothing it out can reduce that problem.
- Lets paint adhere better: Finishing makes it easier for coats of paint to adhere to the surface.
- Reduces friction: Having a smoother surface allows metal parts intended to rotate to do so with minimal resistance, increasing their smoothness and efficiency.
- Increases conductivity: Many metal parts are intended to conduct electricity. The smoother the connection points between two pieces of metal, the better they will conduct.
- Improves appearance: On top of everything else, having a smoother surface helps the object appear cleaner and sleeker.
Without finishing a piece of metal, it can fall prey to any number of problems. If you want your metal parts running smoothly, you’ll need to deburr and finish them — otherwise, they can begin to corrode and experience increased friction with the pieces around them.
Where Can I Find Mass Finishing Equipment?
When you are looking for the right finishing systems for aerospace deburring or mass finishing equipment for another industry, turn to Advanced Deburring and Finishing. We provide high-quality finishing products of all kinds, as well as consulting on how best to use them.
If you require equipment or consultation for your aerospace metal finishing, we’d love to help. Just get in touch with us about your needs. We sell the system — order yours today!